I. Research status at home and abroad
    The research on low-quality potassium-sodium feldspar beneficiation and purification technology is based on the research and industrial application of ceramic raw materials in China's “August 5th†and “Nine-Five†scientific and technological projects. Declining, and ceramics and other industries are proposed against the background of the rapid growth of demand for feldspar, especially high-grade feldspar. With the reduction of Changshi rich ore and the development of comprehensive recovery of feldspar technology in other mines, re-election, electrification, magnetic separation, flotation and other mineral processing methods have been introduced for joint sorting operations to remove associated minerals such as quartz and mica . , the purpose of recycling feldspar concentrate rich in potassium and sodium. In recent years, more work has been done on the purification of feldspar at home and abroad, mainly in the following aspects:
    1.1 crushing and grinding
    The crushing and grinding of feldspar is on the one hand to meet the particle size requirements of the final product, and on the other hand, the need for the impurity removal process. The coarse crushed feldspar mostly uses a jaw crusher, and the broken product is generally about 10mm. At present, there are many researches on the fine crushing and grinding process of feldspar in China, and there are many related equipments, mainly including roller crusher , counter crusher, impact mill, hammer mill, stone grinding and column mill. , tower mill, Raymond mill, agitator mill, vibratory mill, sand mill and jet mill.
At present, Changshi Grinding is mainly divided into dry grinding method and wet grinding method. Relatively speaking, the wet grinding efficiency is higher than that of the dry method, and the phenomenon of “over-grinding†is less likely to occur. From the perspective of the application industry, the processing of feldspar raw materials in the glass industry mostly uses steel rod media grinding, the grinding efficiency is high and the particle size is uniform, but the introduction of iron pollution leads to the low quality of feldspar products; the ceramic industry is due to the raw materials of feldspar The requirements are higher, so stone rim or porcelain ball grinding is often used, the grinding efficiency is low and the energy consumption is high, and high efficiency and process continuous operation cannot be realized. On the basis of ensuring the high quality of feldspar products, achieving high-efficiency grinding and continuous production is an important topic in the research of feldspar processing and purification.
    1.2 Washing and de-sludge
    Washing is suitable for feldspar produced from weathered granite or feldspar sand mine. It mainly removes impurities such as clay , fine mud and mica. On the one hand, it reduces the Fe 2 O 3 content in the feldspar ore , on the other hand, it can improve the feldspar. Potassium and sodium content in the mine. Washing is the use of clay, fine mud, mica and other small particle size or small sedimentation velocity characteristics, under the action of water to separate it from coarse feldspar. Commonly used equipment are Denver scrubbers, vibrating screens, washing tanks, mixing tanks and grinding machines.
The deliming is mainly to remove the primary slime in the ore and the secondary slime produced by grinding, etc., to prevent a large amount of fine mud from affecting the sorting effect of subsequent operations (such as flotation, magnetic separation, etc.). Usually de-sludge in a single or composite force field, commonly used equipment such as mud hopper, centrifuge, hydrocyclone.
    1.3 magnetic separation
    Since the iron minerals, mica and garnet in the feldspar have a certain magnetic property, they can be separated from the feldspar under the action of an external magnetic field. Generally, the iron minerals and mica in the feldspar are weak in magnetism, and only a strong magnetic separation device can obtain a better sorting effect. At present, the domestic magnetic separation equipment for feldspar removal mainly includes: permanent magnet roller type strong magnetic separator, permanent magnet barrel type medium strong magnetic separator, wet type flat ring strong magnetic separator and high gradient strong magnetic separator. .
    ( 1 ) Permanent magnet roller type strong magnetic separator
    The permanent magnet roller type strong magnetic separator adopts the principle of repelling the magnetic pole of rare earth permanent magnet, and is formed by alternately stacking a pair of permanent magnet discs and soft iron discs, and the magnetic induction intensity of the magnetic roller surface can reach 2.0T. The device is suitable for dry sorting of weak magnetic minerals. In recent years, it has become the main equipment for dry removal of feldspar. It is characterized by good sorting effect, low operating cost and convenient operation, but it is subject to the lower limit of material size (generally Limit of 0.12mm).
    ( 2 ) Permanent magnetic cylinder type magnetic separator
    Strong permanent magnet drum magnetic separator is based on a weak magnetic field of permanent magnetic separator degenerate into neodymium-iron-boron permanent magnet material is made, the selection of sub-magnetic flux density is generally 0.3 ~ 0.8T. There are two kinds of equipments, dry and wet, and there are many manufacturers and series. There are ZC (NCT) series magnetic machine of Maanshan Mining Research Institute, DPMS series strong magnetic separator of Changsha Research Institute of Mining and Metallurgy, Guangzhou Nonferrous Metal. It belongs to the ZCT cylinder magnetic separator of the institute. This type of equipment is characterized by both wet and dry, low operating costs, but due to the low magnetic field, it is difficult to obtain high-grade feldspar products.
    (3) Wet flat ring strong magnetic separator
    The wet flat ring strong magnetic separator is a widely used electromagnetic strong magnetic separation equipment for mines at home and abroad, and its background magnetic induction intensity is 1.2 to 1.7T. The Changsha Research Institute of Mining and Metallurgy used the Shp wet magnetic separator to remove the impurities from the Dechang-1mm feldspar mine in Sichuan. The test results show that when the ore contains 0.5% iron, a magnetic separation of 0.2% or less can be obtained. Stone products. The advantage of this equipment is that the selected granularity is wider and the processing capacity of the equipment is larger.
    (4) High gradient magnetic separator
    The high-gradient magnetic separator is the most effective equipment for purifying fine-grained minerals. Its background magnetic induction intensity can reach 2.0T (up to 5.0T abroad), and it can purify -74μm feldspar. The Changsha Research Institute of Mining and Metallurgy uses CRIMM gradient magnetic separator to remove iron from the Pingjiang feldspar mine in Hunan. When the ore contains about 0.2% iron, a feldspar special grade product containing less than 0.05% iron can be obtained by one magnetic separation. The Mingguang feldspar mine in Anhui Province uses the SLon vertical ring pulsation high gradient magnetic separator developed by the Zhangzhou Nonferrous Metal Research Institute to remove impurities. When the ore contains 0.6% iron, a feldspar product containing less than 0.3% iron can be obtained by one magnetic separation. High gradient magnetic separation is an effective way to produce high-grade feldspar products, but equipment costs and operating costs are high.
    1.4 , the progress of flotation technology
    Flotation is an effective way to remove impurities from feldspar. On the one hand, it can remove impurities such as iron and titanium in feldspar. The types of impurities and minerals contained in the ore are different, but the collectors are different. The process is selected; on the other hand, the separation of feldspar and quartz can be achieved, thereby increasing the potassium and sodium contents. At present, more research is on the separation of feldspar and quartz, as well as the selective separation of potassium feldspar and albite.
    (1) Flotation of titanium-containing gangue minerals
    Studies have shown that titanium in feldspar minerals is mainly present in rutile (or anatase) and a small amount of vermiculite. In the range of pH 4-6, using fatty acid as a collector, rutile (or anatase) is very easy to float, but its floatability is decreased in the following order: oleic acid > linoleic acid > linolenic acid . With petroleum sulfonate or fatty primary amine acetate, rutile (or anatase) can also be floated under acidic conditions of pH 2.5 with better selectivity. It is also possible to use potassium hydroxamate or to mix succinic acid amide salt with a sulfonate to use flotation rutile (or anatase). At present, there is only a small amount of literature on the flotation performance of vermiculite, indicating that vermiculite can be floated with oleic acid and its soap, but this flotation process is very sensitive to the presence of slime.
    (2) Flotation of iron-bearing minerals
    In general, iron in feldspar minerals mainly occurs in mica, pyrite, a small amount of red limonite and iron-containing alkali metal silicates (such as garnet, tourmaline and amphibole). Generally, under acidic conditions of pH 2.5-3.5, mica can be floated with an amine-based cation collector; under acidic conditions of pH 5-6, a yellow drug-based collector can be used to float flotation of pyrite. Mineral; ferric silicate can be floated with a sulfonate collector under acidic conditions of pH 3-4.
    (3) Quartz-feldspar flotation separation technology
    The traditional method of quartz-feldspar flotation separation is the HF acid method, also known as the "fluorine and acid" method, which uses HF acid to adjust the pH to below 2.5 to inhibit quartz, activate feldspar, and realize the separation of feldspar and quartz. However, due to environmental problems and the inconvenience of the use of HF acid, many mineral processing workers are actively studying the fluorine-free separation scheme. In the quartz-feldspar fluorine-free flotation separation process, the most mature and widely used is the fluorine-free acid method, but this process requires strong acidic medium conditions, resulting in serious equipment corrosion. Therefore, the fluorine-free acid-free method and other processes are the future development direction of quartz-feldspar flotation separation process.
    (4) Flotation separation of potassium feldspar and albite
    The separation of K-feldspar (ortho-feldspar and micro-plagioclase) and albite is a challenging topic because most of their mixing occurs in feldspar deposits, which have similar chemical structures and similar physical chemistry. nature. In the late 1960s and early 1970s, Russian researchers used different salts as regulators in HF media to float different types of feldspar: Yanis suggested using magnesium and calcium ions in amine flotation in HF media. As an inhibitor of albite, enriched with potassium feldspar; Starikova uses fluoride for flotation of albite and potassium feldspar in the presence of 15 mg/L NaCI; according to Revnivtzev et al., potassium ions are similar to potassium radii Ions (such as Rb, cs, and Ba) inhibit potassium feldspar, while Na, Ca, Sr, and Mg inhibit albite and anorthite; Mariu conducts amines on pegmatites with equal amounts of albite and feldspar In the flotation test, the best results were obtained with NaCI inhibition of albite: Demir et al. demonstrated that sodium ions inhibit sodium albite when flotation of alkaline feldspar with an amine collector in the neutral pH range.
    Based on the above findings, with the continuous reduction of Changshi rich ore resources, a large number of low-quality feldspar minerals have yet to be developed, and the research of mineral processing and purification technology is the key to improving the utilization rate and product quality of feldspar resources. The traditional feldspar beneficiation process has many problems such as low grinding efficiency, backward technology and equipment, and has become an important factor in restricting the large-scale and large-scale processing of Changsha. Therefore, according to the type and nature of the original ore, determining a reasonable beneficiation process, selecting advanced production equipment, and using high-efficiency and low-pollution flotation reagents have become the breakthrough to solve the above problems. It is the future development trend of feldspar beneficiation to achieve high efficiency of beneficiation, high quality of products and new equipment and equipment.
    Second, the development trend of feldspar removal and purification
    As the demand for high-grade feldspar concentrates is increasing, but there are fewer and fewer high-grade ore concentrates, there is a need for a more efficient and cost-effective method of removing iron. At present, the combined process is easier to obtain high-grade concentrates, and for feldspar ore with extremely high iron content, it is economical to carry out pretreatment such as acid leaching and stripping.
    Bioleaching has the advantages of simple operation and low environmental pollution. Foreign scholars have used it together with other methods to obtain high-purity feldspar concentrates with less than 0.02% iron. There are few studies in this area in China.
    2. 1 bioleaching
    Iron can be used as an electron carrier and energy source for certain microorganisms. When it reacts with microorganisms, it undergoes oxidation and reduction reactions and becomes an ionic state that can be dissolved. The organic acid produced in this process also dissolves the impurity minerals, and then it can be washed by water. Impurity minerals are removed. For iron-containing minerals in extremely slender stone particles, it is difficult to remove by conventional methods, and bioleaching can achieve better results. Microorganisms are not only beneficial to the decomposition of feldspar ore, but also effectively remove iron minerals from the surface of feldspar. Iveta Styriakova conducted an in-depth study of this method, reducing Fe 2 O 3 from 0.175% to 0.114% and TiO 2 from 0.02% to 0.018% by microbial leaching ; studies have also shown that dissolved and removed iron is initially The amount of iron in the feldspar ore is not directly proportional, but also depends on the geological changes of feldspar, the mineral composition and the distribution of iron minerals. Therefore, in order to obtain high quality feldspar concentrate, other methods are needed in combination with microbial treatment.
    Iveta Styriakova and other pre-treatment of differentiated granite-type feldspar ore with heterotrophic bacteria Bacillu spp, and then using oxalic acid acid leaching to remove iron-containing compounds, achieved good results, the organic acid produced by Bacilus spp acts between mineral particles and The iron-impregnated iron compound of the gap towel dissolves and releases iron ions. This pre-treatment not only benefits the further action of oxalic acid, but also greatly reduces the use concentration and recovery cost of oxalic acid, and the pollution discharge is also reduced. The iron removal method combining heterotrophic bacteria with strong magnetic separation was studied, and the iron removal rate was up to 70%.
    2. 2 joint process
    Some high-speed rails are extremely difficult to select feldspar mines, which are not only high in iron, but some of them are infiltrated in the feldspar cleavage form by iron dyeing. For these minerals, if a single sorting process cannot meet the requirements of concentrates , a joint process can be used.
    (1) Magnetic-floating joint process
    Guo Baowan and others conducted iron removal test on high-speed iron silicate feldspar mine. The iron content was reduced by more than 1% compared with single magnetic separation and flotation process in the magnetic separation-flotation combined process. Most of the iron minerals are removed by magnetic separation, and the fine iron minerals and iron-dyed potassium feldspar are removed by flotation. The potassium feldspar concentrate is much lower than the single magnetic iron, which is much lower than the single flotation concentrate. The iron grade is also low, and the yield is close. The best sorting effect can be obtained after the first dry magnetic separation, but the industrial thousand magnetic separation needs to be dehydrated and dried, and the cost is relatively high, so after the wet magnetic separation The process of flotation is more widely used.
    (2) Stripping - strong magnetic separation process
    Strong magnetic field magnetic separation-flotation combined process can obtain qualified feldspar concentrate products, but the process is more complicated, so equipment investment and ore dressing costs are higher. If the feldspar mine has the characteristics of soft and easy pulverization, it can be used to grind the ore after crushing and de-sludge to remove a small amount of steel balls in the mill to remove the iron minerals contained in the mica minerals, and feldspar. The minerals are not crushed. The results show that a good separation index can be obtained by using a strong magnetic field desorption method. Compared with the magnetic-floating process, the process has a high yield of feldspar concentrate, and has the characteristics of simple process and low beneficiation cost.
    (3) A two-cycle flotation process
    OY Gulsoy et al. used a two-cycle process to remove mica, titanium and iron oxides from a certain albite in Turkey. First, the mica was removed by reverse flotation with an amine ion (Armac TD) collector at a pH of 2.5 to 3. Secondly, the titanium and iron oxides were removed by sodium oleate at a pH of 5.5 to 6.5. . The TiO 2 +Fe 2 O 3 in the feldspar concentrate can be reduced to 0.12% or less under the optimum conditions of the amount of collector, grinding fineness and pH . This process can be used to promote industrial applications and also to obtain feldspar concentrates that meet commercial requirements.
    (4) Scrubbing and flotation process
    The -2mm grinding product is scrubbed and divided into two grades of -2+0.25mm and -0.25mm. The former grade product can be used as ceramic tile, and the latter grade product cyclone is de-sludged. The flotation of the feldspar concentrate can be obtained by flotation.
A relief valve, a hydraulic pressure control valve. In hydraulic equipment, it plays the role of constant pressure overflow and safety protection. Constant pressure overflow function: in a quantitative pump throttle regulation system, a quantitative pump provides a constant flow rate. When the pressure of the system is increased, the flow demand will be reduced. At this time the overflow valve is opened to overflow the excess flow back to the tank and ensure the inlet pressure of the overflow valve, that is, the outlet pressure of the pump is constant (the valve mouth is often opened with the pressure fluctuation). The components that easily produce noise in the hydraulic device are generally considered to be pumps and valves, and the main valves are overflow valves and electromagnetic reversing valves. There are many factors to produce noise. The noise of the overflow valve consists of two kinds of sound and mechanical sound. The noise in the velocity sound is mainly caused by the vibration of oil, the hole and the hydraulic shock. In mechanical sound, it is mainly caused by the impact and friction of the parts in the valve.
DAEWOO/DOOSAN |
DH50-7, DH55D, DH60-7, DH80, DH130, DH150, DH150W-9, DH215-5, DH200-5, DH150LC-7, DH215-7, DH220-5, DH220-7, DH220-9, DH220-10, DH225-9, DH258, DH258LC-7, DH280, DH290B, DH300-5, DH300-7, DH320, DH360, DH370, DH500, DX300 |
HYUNDAI |
R60-7, R80, R130, R140, R150-7, R150-9, R1107-7, R160-7, R210, R220, R220-7, R215-7, R220-5, R225-7, R225-9T, R225lc-7, R290, R350-7,R110-9, R215-9, R275LC-9, R305, R305-7, R320, R335-7,R360, R370, R375, R375-7H, R455, R460, R485-7 |
VOLVO |
EC130, EC140B, EC210B, EC210C, EC235C, EC240B, EC290, EC290B, EC290C, EC360B, EC460B, EC460C, EC480D |
CAT |
E305, E320, E325C, E315C, E330C, E315D, E320D, E325D, E330D, E360D, E70B, E120B, E200B, E320B, E330B |
KOMATSU |
PC35,PC40,PC45, PC50, PC55, PC60,PC60-6, PC70, PC75, PC78, PC80, PC90, PC100, PC110, PC120, PC120-7,PC130, PC150, PC160, PC180, PC200,PC200-6, PC200-7,PC200-8, PC210-8,PC220-6,PC220-7,PC210, PC220, PC230, PC240,PC240-8, PC270, PC300, PC360,PC360-7, PC350, PC400, PC450, PC650, PC750, PC1250,D31, D50,D65, D85, D155, D275, D375, D475 |
HITACHI |
EX200-2, EX220-2, EX120-5, EX200-5, EX220-5, EX400-5, ZAXIS200-3, ZAXIS210-3, ZAXIS240-3, ZAXIS 270-3, ZAXIS330-3, ZAXIS360-3, ZAXIS110, ZAXIS120, ZX200-6 |
KOBELCO |
SK200-3, SK200-5, SK135rs, SK70rs,SK60,SK120-5, SK200-8, SK250-8, SK260-8, SK130-8, SK200-6e, SK210-6e, SK160 |
KATO |
HD80R, HD820-5, HD1023, HD1430, HD700-7,HD1430-7, HD1250-7, HD450-7 |
SUMITOMO |
SH120A2/A3,SH130, SH200A2/A3, SH210A5, SH240A3, SH360A5 |
KUBOTA |
KX155, KX135, KX161-3 |
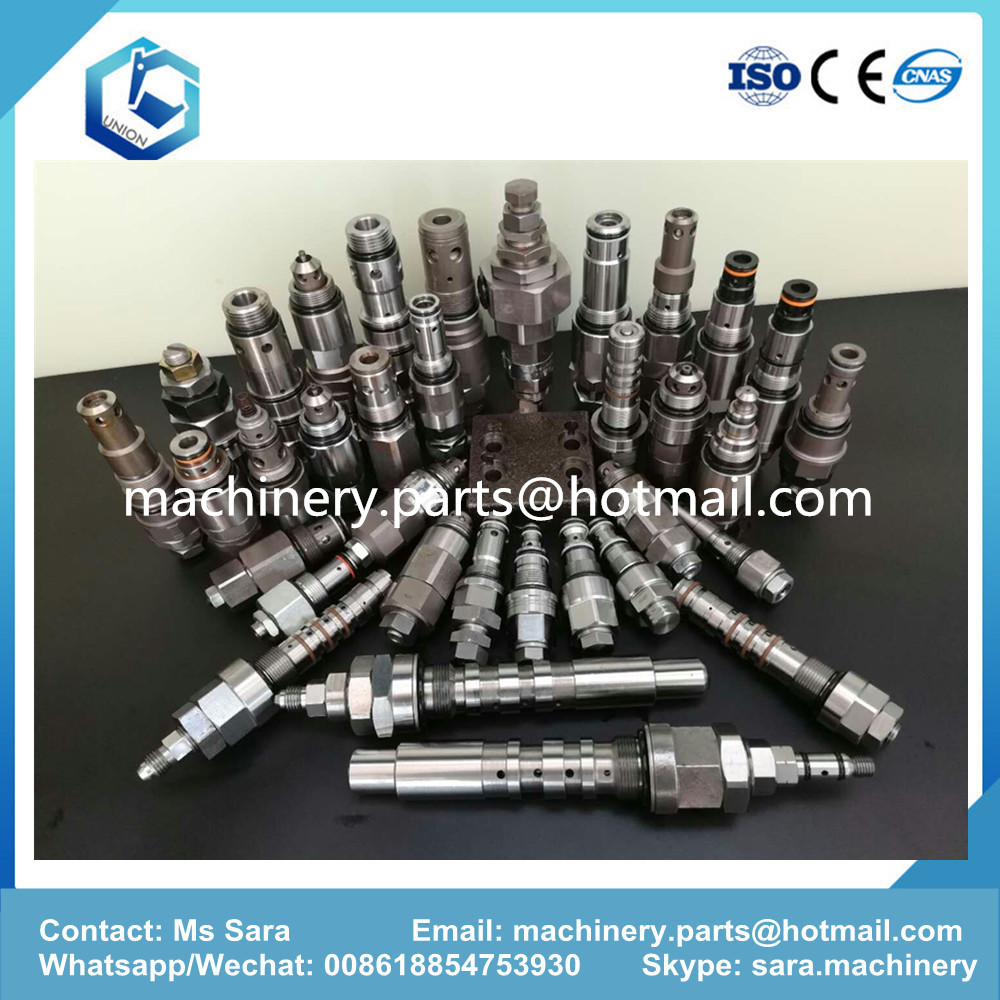
Excavator Relief Valve,Pc200-7 Excavator Relief Valve,Pc200-8 Excavator Relief Valve,Pc300-7 Excavator Relief Valve
JINING UNION MACHINERY AND PARTS CO., LTD. , https://www.vmpmachineryparts.com